Different materials rolls and the cutting tools solutions
Part 1 Different materials rolls and the hardness
No. |
Rolls Materials |
Hardness |
1 |
High Ni-Cr Cast Iron Rolls |
HSD76~82 |
2 |
Hi Chromium Cast Iron Rolls |
HSD72~82 |
3 |
Semi-Steel Rolls |
HSD55~65 |
4 |
Chilled Cast Iron Rolls |
HSD50~70 |
5 |
Hi-Carbon Semi-Steel Rolls |
HSD65~72 |
6 |
High Speed Steel Rolls(HSS Rolls) |
HSD82~90 |
7 |
Hi-Cr Cast Steel Rolls |
HSD68~75 |
8 |
Tungsten Carbide Ring |
HRA88 |
9 |
Forged Steel Cold Rolls |
HSD92~105 |
Part 2 Roll classification and common processing difficulties
According to the level of hardness classification
1. Low hardness rolls processing characteristics and tool selection: Such as ductile iron roll, high alloy cast iron roll, they commonly used in hot roll, Supporting roller, middle roller. Compare with
working rolls, their characteristics are low hardness. Turning this type rolls, you can choose carbide insert.
2. Processing characteristics of high hardness rolls and tool selection: such as machining chilled cast iron Rolls (ICDP Rolls), High nickel chromium cast iron rolls, high boron steel rolls, HSS Rolls, Semi-steel rolls (casting semi-steel rolls and high carbon semi-steel rolls),Ni-Cr-Mo centrifugal composite rolls. Because of its high hardness, these rolls blank usually has stomatal, sand, ect defects. And it requires high on the cutting tools performance, such as impact resistance, heat-resistance, wear resistance,ect.
Part 3 The cutting tool mateirals that can be used for machining rolls
(1) Diamond Inserts (PCD inserts):the hardness is about HV4000~7000, and it is suitable for machining Non-ferrous metals and other non-metal materials. And PCD Inserts are often used for milling the tungsten carbide rolls.
(2) Cermaic Inserts: In the past, many manufactuers used ceramic inserts for machining rolls. However, when meet bad working environment, the rolls will be easily chipping, and not work stable.
(3) Carbide inserts: the hardness is HV1350~1800, and used in many fields, but the tool life will be low, most of the customers would like to replace them instead of cbn inserts.
(4) CBN Inserts: the hardness of cbn is only second to pcd inserts, and is the main cutting tools materials for machining rolls.
Part 4 Cutting tool application case of machining rolls with CBN Insert
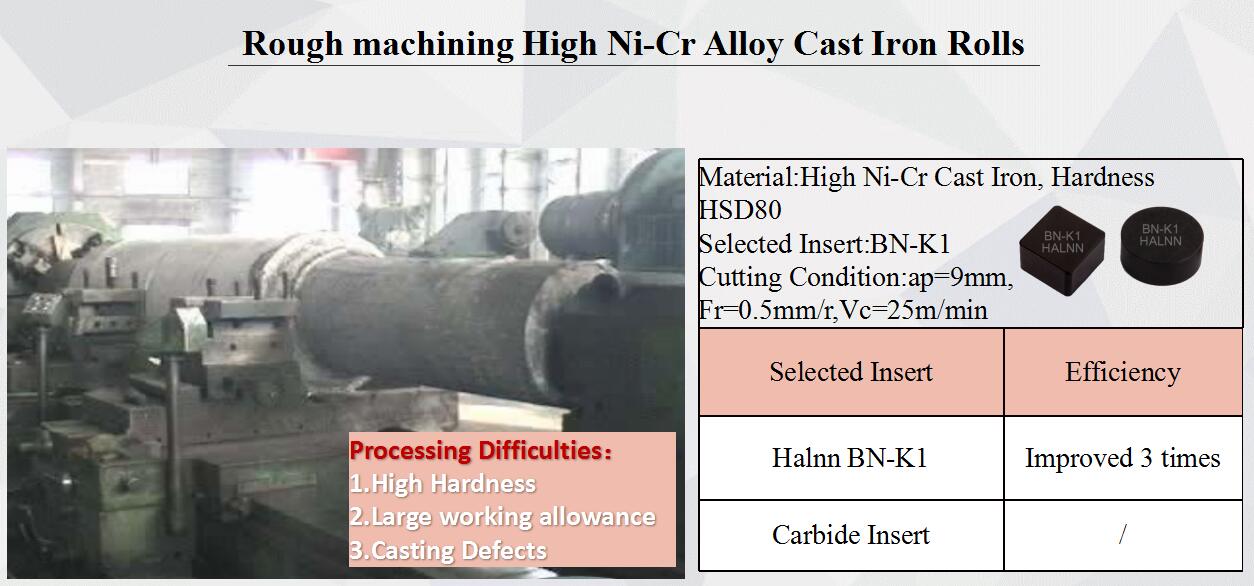

Part 5 The corresponding tool holder for machining rolls
Part 6 The recommend cutting parameters of machining rolls for reference
No. |
Rolls Materials |
Hardness |
Select CBN Insert |
Recommend Cutting Condition |
Vc(m/min) |
ap(mm) |
Fr(mm/r) |
1 |
High Ni-Cr Cast Iron Rolls/Hi-Cr Cast Iron Rolls |
HSD60~80 |
BN-K1 |
40~60 |
2~10 |
0.5~1.5 |
60~90 |
1 |
0.5~1.0 |
2 |
Cast Semi-SteeRolls |
30~60 |
1~10 |
0.5~1.5 |
50~80 |
1 |
0.5~1.0 |
3 |
High Carbon Semi-Steel Rolls |
35~50 |
3 |
0.5~1.5 |
4 |
Chilled Cast Iron Rolls |
25~50 |
1~10 |
0.5~1.5 |
3 |
High Speed Steel/HSS Rolls |
HSD85~92 |
BN-S20 |
20~45 |
4 |
0.5~1.5 |
8 |
Tungsten Carbide Ring |
HRA88 |
BN-S30 |
10~15 |
1 |
0.3~0.7 |
9 |
Forged Steel Cold Rolls |
HRC65 |
BN-S20 |
10~25 |
0.2~7 |
/ |
If you would like to know more details or have any problems on machining rolls, please feel free to contact with us info@halnntools.com, Whatsapp:+8615617635382