Many people in machinery factories don't know what a CBN tool is.but don't know the processing field and its suitable materials, so this
time Halnn will give you a brief introduction to the definition and application of CBN tools. We hope everyone can understand and choose
the right tool material for cutting when machining the workpiece. To meet the needs of customers to reduce costs and increase efficiency.
1. What is a CBN tool?
The CBNtool is synthesized by CBN micropowder and a small amount of binder under high temperature and high pressure conditions. Its
hardness is second only to diamond and much higher than other materials. Therefore, it is collectively referred to as a superhard tool.
CBN tools have high hardness, thermal stability and chemical inertness. Their thermal stability is much higher than that of diamonds. They
have greater chemical stability to iron-based metal elements and are therefore often used for the cutting of ferrous metals.
The use of CBN tools is a major contribution to metal processing, leading to revolutionary changes in cutting, and is the second leap in
cutting technology.
2,The structure of the CBN tools.
According to the structure, it is divided into a brazed CBN tools and solid CBN tools
The brazed CBN tools are welded from a CBN material to a cemented carbide substrate to form a variety of turning inserts or other boring
inserts, primarily for finishing operations.
The solid CBN tools are made of CBN material, and there is no hole in the middle. It needs professional arbor to match, mainly used for
roughing process.
3,The processing material of CBN tools.
As mentioned above, CBN tools are often used for the cutting of ferrous metals, mainly including high-hardness cast iron/cast steel/forged
steel, hardened steel, ordinary gray cast iron, powder metallurgy and other difficult-to-machine materials (hardness requirements of steel
parts above HRC45).
(1) High hardness cast iron / cast steel / forged steel: such as high chromium cast iron, alloy cast iron, nickel hard cast iron, high manganese
steel, high speed steel(HSS) and other materials can be processed, such as rolls, slurry pump casing, Impellers, guards, linings, etc. are typical
components. The processing of such workpieces mainly uses solid CBN inserts, which can cut the blank margin with a large margin, improve
production efficiency and reduce the total production cost, such as Halnn BN-K1 CBN grade inserts rough roll blanks, The cutting depth not only
does not collapse, but also can withstand the impact of surface casting defects to ensure surface quality.
(2) Hardened steel: such as quenching gear/gear shaft, bearing, mold, synchronizer, ball joint universal joint, quenching roll and other components
are typical quenching parts, hardness is about HRC60, CBN tools can be easily solved. And to ensure a high surface finish, such as Haln BN-H21
CBN grade inserts strong intermittent cutting hardened gear, not only does not collapse the knife and obtain a higher surface finish.
(3) Gray cast iron: such as engine block, cylinder head, brake disc, brake drum, pulley, clutch platen, etc. are all gray cast iron material. The use
of CBN tools can replace the high-speed cutting of traditional carbide tools. The cutting speed can be several times higher than that of traditional
carbide tools. On the basis of ensuring high surface quality, the tool life is 10-20 times for traditional carbide tools, such as Halnn BN-K20 CBN
grade inserts fininshing car brake disc, compared with the production of the coated blade to increase the beat by 50%
(4) Powder metallurgy: due to its own porous structure, the particle hardness of the parts is as high as HRC60, which is easy to cause edge fatigue
and micro-crack during processing. The CBN tools can effectively improve the production efficiency and ensure the tool life, such as Halnn BN-K10
CBN grade inserts processing powder metallurgy pulley not only reduces the number of passes, improves production efficiency, but also has the same
life span as other cubic boron nitride inserts, reducing production costs.
4, The application of CBN tools.
(1) High-speed cutting: mainly reflected in the field of ordinary gray cast iron. Due to the rising price of raw materials for gray cast iron, competition
with enterprises has gradually increased. The maximum line speed of gray cast iron initially processed with traditional carbide inserts should not
exceed 350 m/min, and vice versa. However, the maximum linear speed of gray cast iron processed by CBN tools can reach 1500m/min (on the
basis of machine rigidity), and high wear resistance and high surface quality of the workpiece to be machined are ensured.
(2) Heavy-duty cutting: mainly in the field of high-hardness cast iron/cast steel, such as roll and pump materials used in
large-scale equipment, large blank machining allowance, and need for cutting tools with excellent wear resistance and impact
toughness, and the CBN tools can reach a depth of 10mm at a time, greatly improving production efficiency.
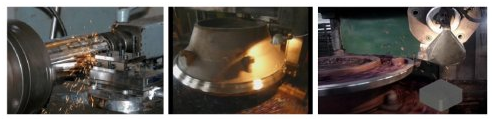
(3) Dry cutting: Regardless of which type of material is processed, the CBN tools are processed by dry cutting. The CBN tools
have high temperature and red hardness and can withstand normal cutting at a high temperature of 1200 °C. Guarantee
excellent durability. Moreover, it reduces the unnecessary cost of machining the workpiece with the cutting fluid and ensures
a good production environment.